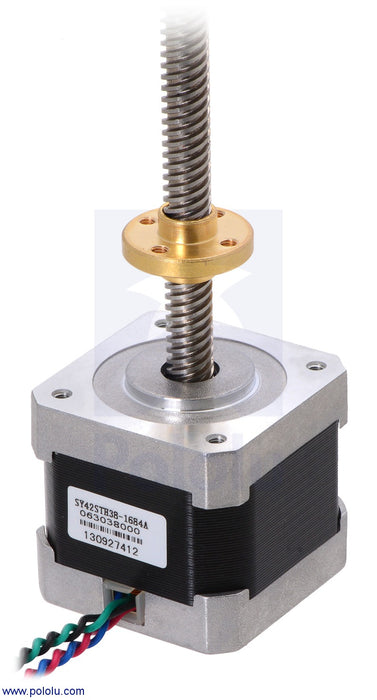
Stepper Motor with 28cm Lead Screw: Bipolar, 200 Steps/Rev, 2.8V, 1.7 A/Phase
All prices are VAT included
This NEMA 17-size hybrid bipolar stepping motor has an integrated 28 cm (11″) threaded rod as its output shaft, turning it into a linear actuator capable of precision open-loop positioning. The included traveling nut has four mounting holes and moves 40 µm (1.6 mil) per full step; finer resolution can be achieved with microstepping. The stepper motor has a 1.8° step angle (200 steps/revolution) and each phase draws 1.7 A at 2.8 V, allowing for a holding torque of 3.7 kg-cm (51 oz-in).
This linear positioning drive consists of our 42×38 mm NEMA17 stepper motor with a built-in lead screw in place of the normal output shaft, which makes it easy to move an object or platform in a linear motion with the precision of a stepper motor . Motors like this are especially popular for use in home-built 3D printers (eg RepRap) and CNC machines. The stainless steel threaded rod extends 28 cm (11″) from the face of the stepper motor, and since it is integrated into the motor itself, you do not have to deal with bulky shaft couplers or loose set screws.
The included copper alloy traveling nut (also known as a carriage nut) features a mounting flange with four holes threaded for M3 screws. The nut moves 8.0 mm per full revolution of the lead screw, which allows for a linear resolution of 0.040 mm per full step of the stepper motor. Even smaller step sizes can be achieved through microstepping, which is a feature of many bipolar stepper motor drivers. We recommend the DRV8825 stepper motor driver carrier for use with this stepper motor, which allows for a linear resolution of 1.25 µm per 1/32 microstep. However, please note that the nut is not spring loaded, so changes in direction will result in loss of positioning precision due to backlash.
The maximum achievable linear speed depends a lot on the details of the system, including the load and motor supply voltage. Under ideal conditions (eg with gradual ramping up of the step rate, a high supply voltage, and no load), we were able to achieve speeds close to 30 cm/s (12 in/s).
The stepper motor has a 1.8° step angle (200 steps/revolution) and each phase draws 1.7 A at 2.8 V, allowing for a holding torque of 3.7 kg-cm (51 oz-in). The motor has four color-coded wires terminated with a JST XHP-4 connector with 0.1" spacing: black and green connect to one coil; red and blue connect to the other. It can be controlled by a pair of suitable H-bridges ( one for each coil), but we recommend using a bipolar stepper motor driver.
Specifications
- Size: 42.3 mm square × 38 mm, not including the shaft (NEMA 17)
- Weight: 385 g (13.5 oz)
- Shaft diameter: 8 mm threaded rod
- Shaft length: 28 cm (11″)
- Steps per revolution: 200
- Linear step size: 40 µm (1.6 mil) per full step
- Current rating: 1.68 A per coil
- Voltage rating: 2.8V
- Resistance: 1.65 Ω per coil
- Holding torque: 3.7 kg-cm (51 oz-in)
- Inductance: 3.2 mH per coil
- Lead length: 16cm (6.5″)
- Output shaft supported by two ball bearings
More specifications are available in the datasheet (63k pdf).